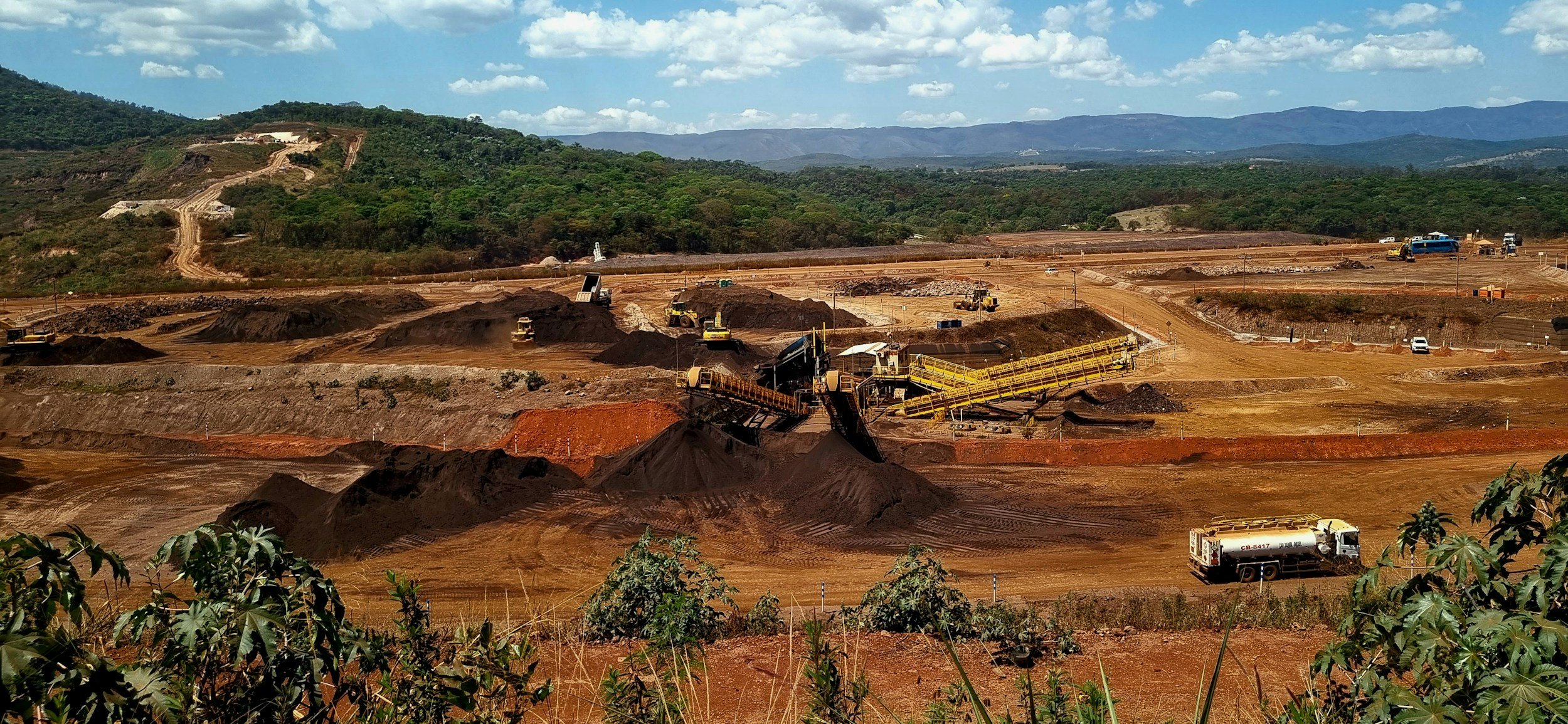
-
ForeSite AI for Mining
In the challenging and resource-rich environment of West Africa, the mining industry plays a crucial role in economic development. Leveraging advanced technologies such as computer vision is revolutionizing the way mining operations are conducted, ensuring higher efficiency, safety, and profitability. This page outlines how ForeSite AI is applying cutting-edge computer vision technologies to transform the mining industry in West Africa.
-
Enhanced Ore Grade Monitoring and Sorting
Traditionally, ore grade monitoring and sorting have relied heavily on manual processes or basic automation, often leading to inefficiencies and inaccuracies. By deploying advanced computer vision systems, mining operations in Africa can now automatically analyze and classify ores based on visual data. These systems use high-resolution cameras and machine learning algorithms to identify valuable minerals in real-time, significantly reducing the amount of waste and improving overall yield.
Key Benefits:
Increased Precision: Accurate identification and sorting of high-grade ores, minimizing waste.
Cost Efficiency: Reduced processing costs by minimizing the handling of low-grade materials.
Real-Time Decision Making: Immediate feedback and adjustments during the mining process.
-
Automated Equipment Monitoring and Maintenance
Mining operations are heavily reliant on complex machinery, and any unexpected downtime can lead to significant financial losses. Computer vision technologies enable the continuous monitoring of equipment, detecting potential issues before they lead to failure. By analyzing video feeds and images, our systems can identify signs of wear and tear, overheating, or other mechanical issues, allowing for timely maintenance and reducing the risk of breakdowns.
Key Benefits:
Preventative Maintenance: Early detection of equipment issues to prevent costly downtimes.
Improved Safety: Reducing the risk of accidents caused by equipment failures.
Extended Equipment Lifespan: Prolonged machinery life through timely maintenance and care.
-
Worker Safety and Hazard Detection
The safety of workers in mining environments is a top priority, especially in the often harsh and unpredictable conditions of West Africa. Computer vision systems are employed to monitor safety compliance and detect potential hazards in real-time. These systems can identify when workers are not wearing proper safety gear, detect hazardous conditions like falling rocks, and even monitor worker fatigue, thereby reducing the risk of accidents.
Key Benefits:
Enhanced Safety Compliance: Ensuring that all safety protocols are followed strictly.
Real-Time Hazard Detection: Immediate alerts to potential dangers, preventing accidents.
Worker Fatigue Monitoring: Identifying signs of fatigue to prevent accidents caused by human error.
-
Environmental Monitoring and Management
Environmental impact is a critical concern in the mining sector, and companies are under increasing pressure to minimize their footprint. Computer vision technology assists in environmental monitoring by analyzing visual data to track changes in the landscape, detect illegal mining activities, and monitor water and air quality. This allows mining companies to take proactive measures to mitigate environmental damage and comply with regulatory requirements.
Key Benefits:
Sustainable Operations: Minimizing environmental impact through continuous monitoring.
Regulatory Compliance: Ensuring adherence to environmental regulations and standards.
Proactive Environmental Management: Taking timely action to address environmental concerns.
-
Autonomous Vehicle and Drone Operations
The implementation of autonomous vehicles and drones equipped with computer vision technology is transforming how mining operations are conducted in West Africa. Drones can be used for aerial surveys, providing detailed topographic maps and real-time data on site conditions. Autonomous vehicles, guided by computer vision, can navigate the challenging terrains of mining sites, transporting materials and conducting routine tasks without the need for human intervention.
Key Benefits:
Increased Efficiency: Autonomous operations reduce the need for manual labor and increase operational speed.
Enhanced Safety: Minimizing human presence in dangerous areas reduces the risk of accidents.
Real-Time Data Collection: Drones provide up-to-date information on site conditions, aiding decision-making.
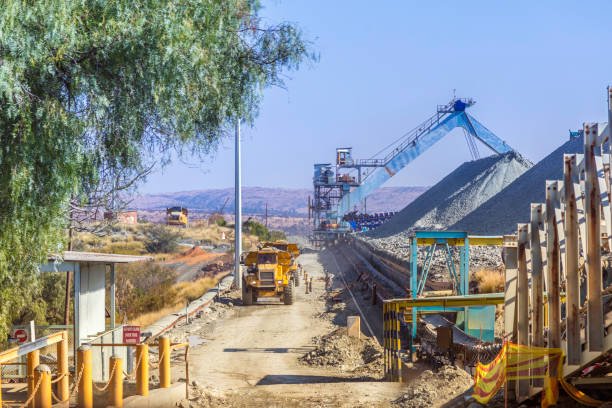
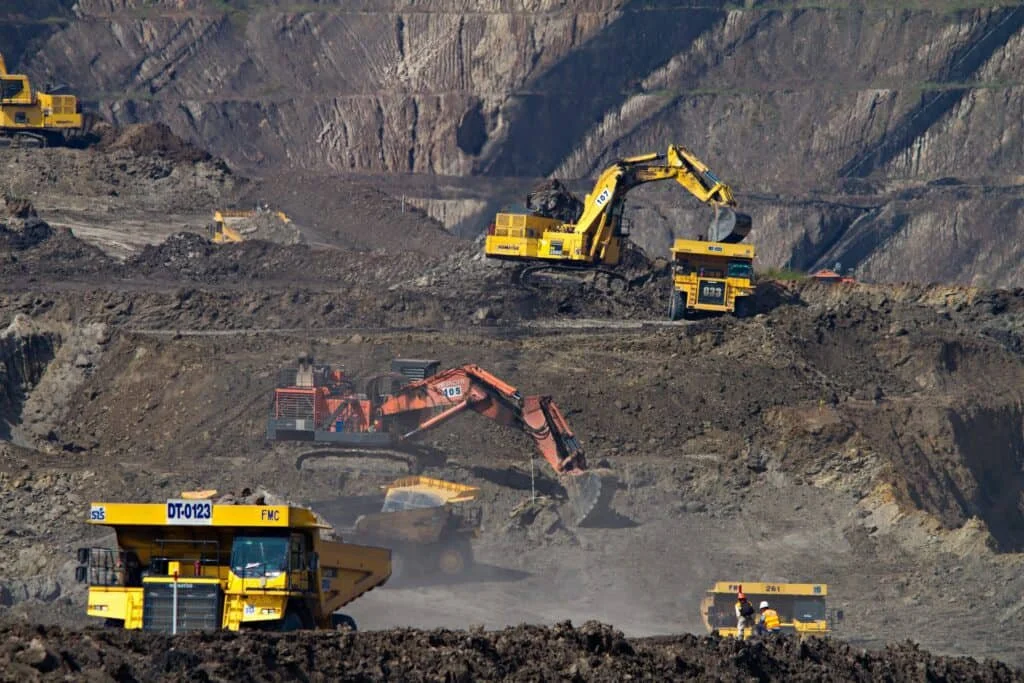

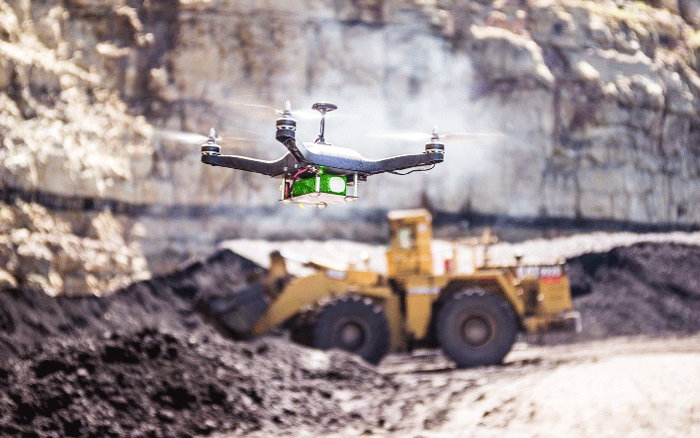
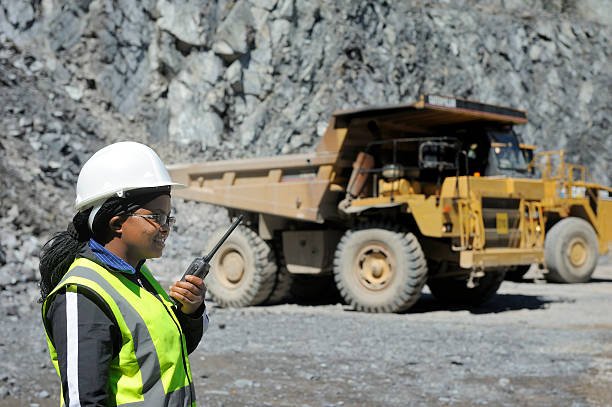
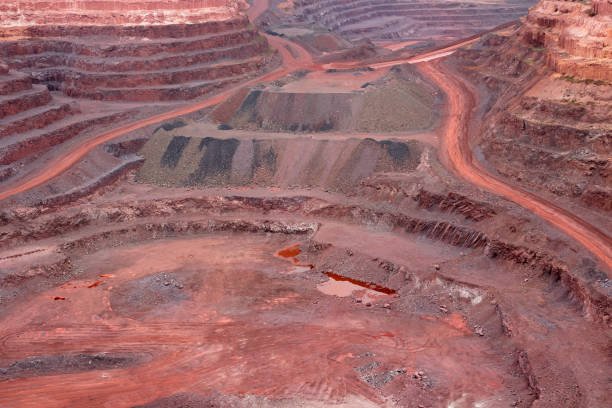
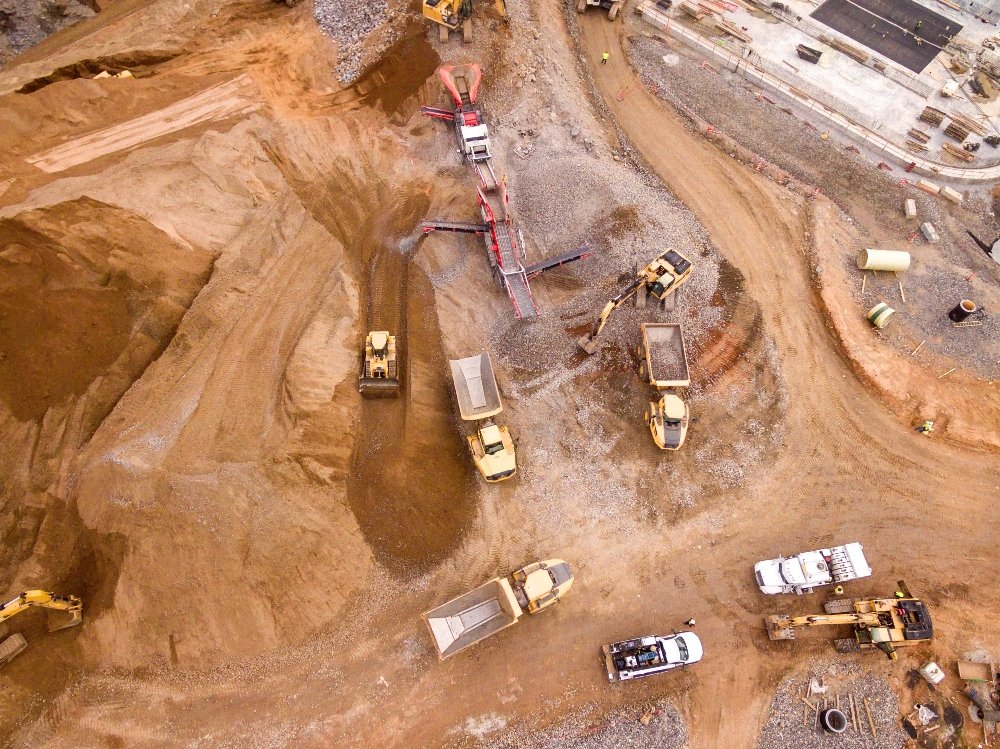

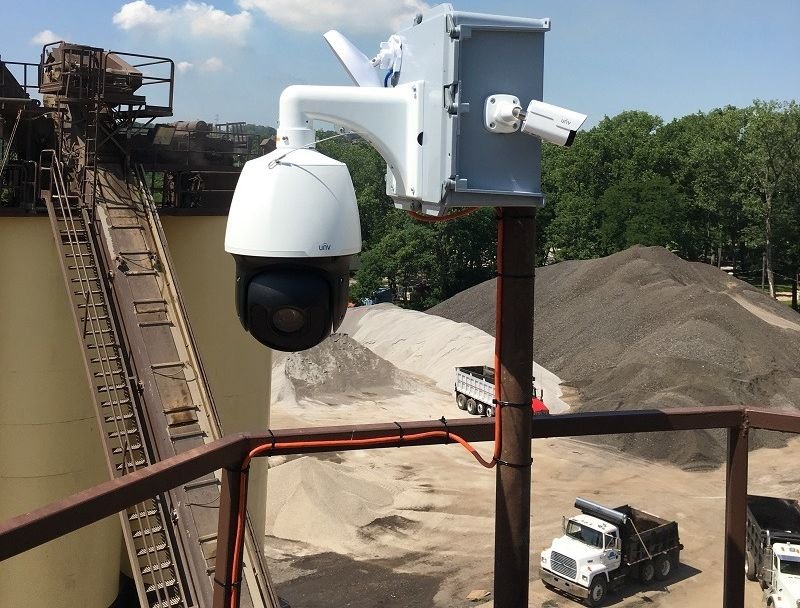

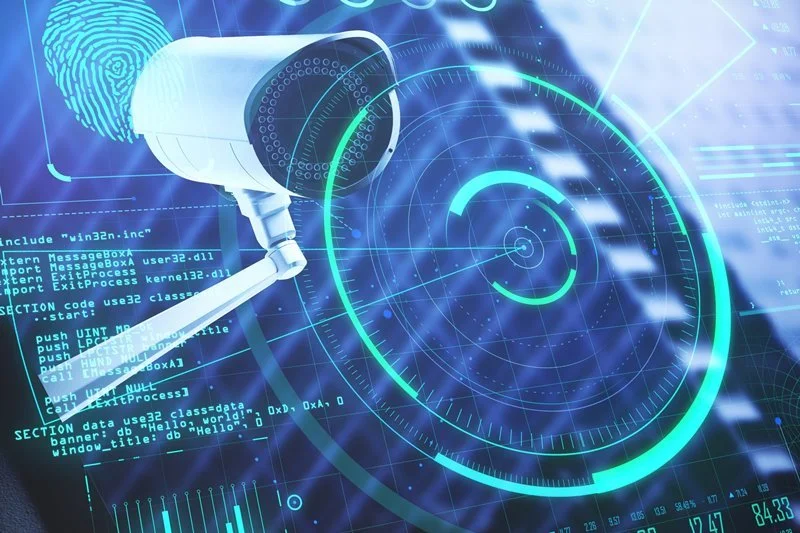
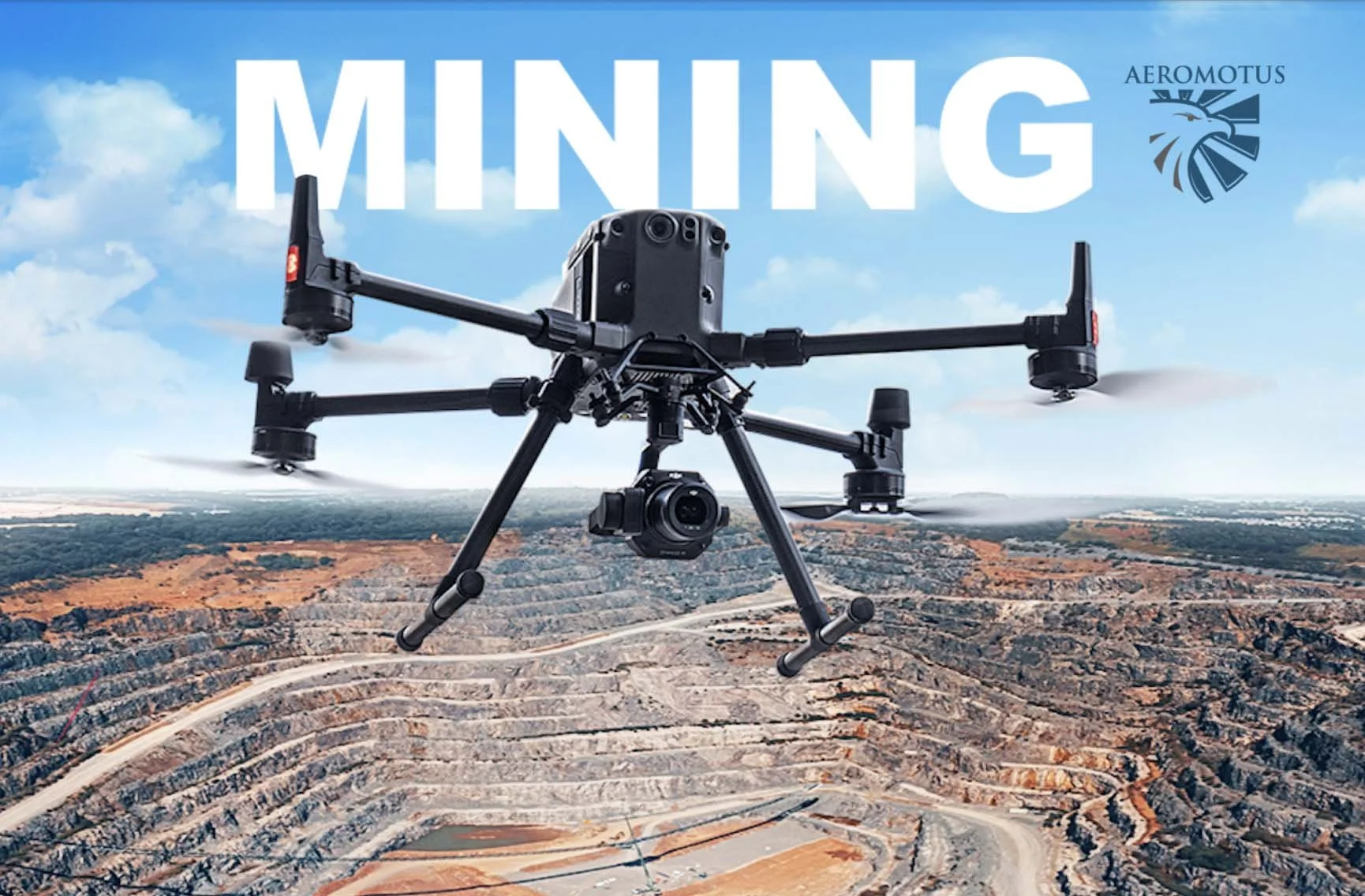
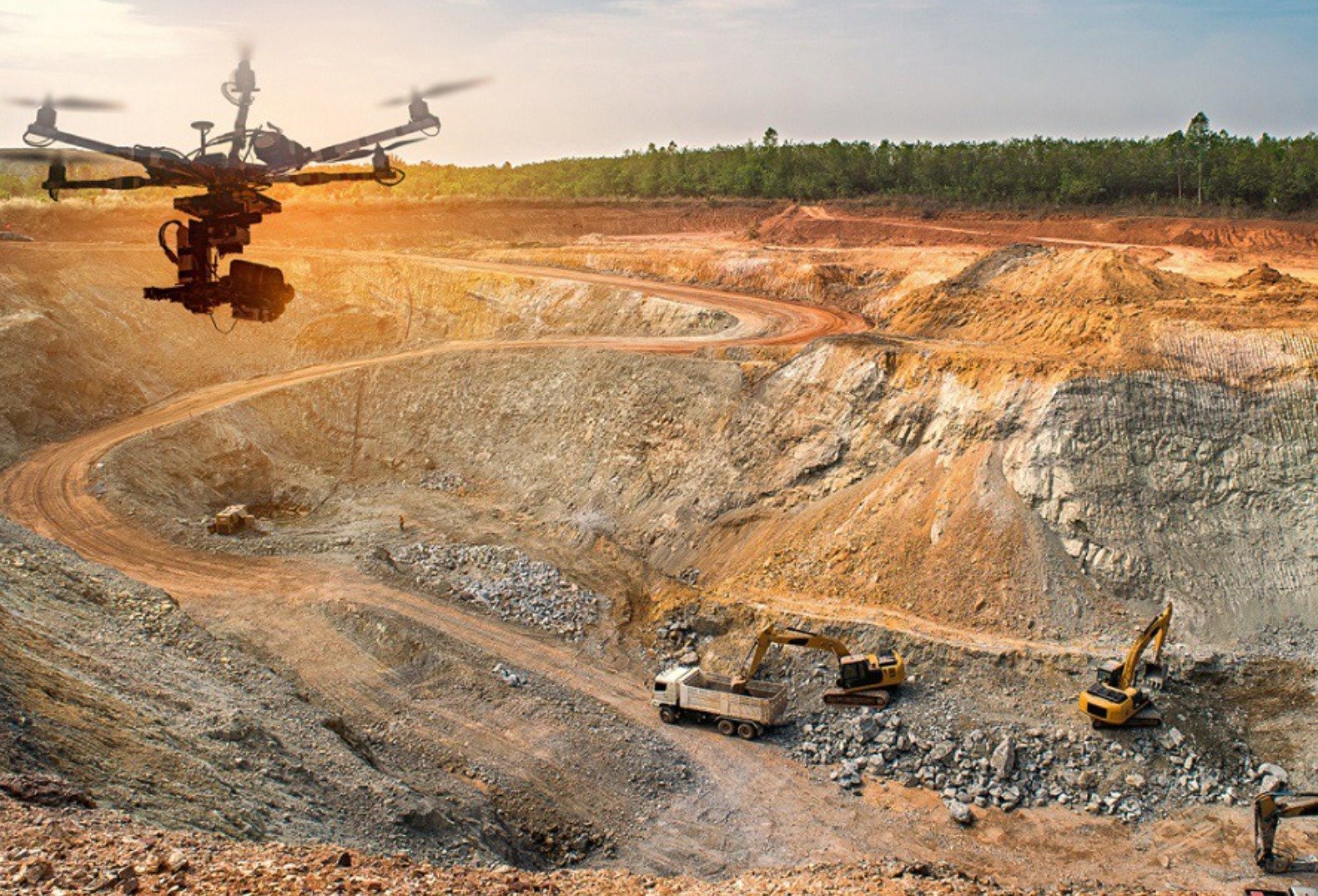
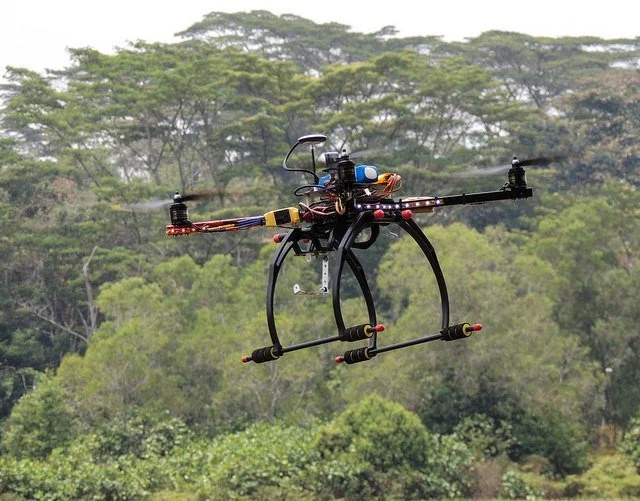
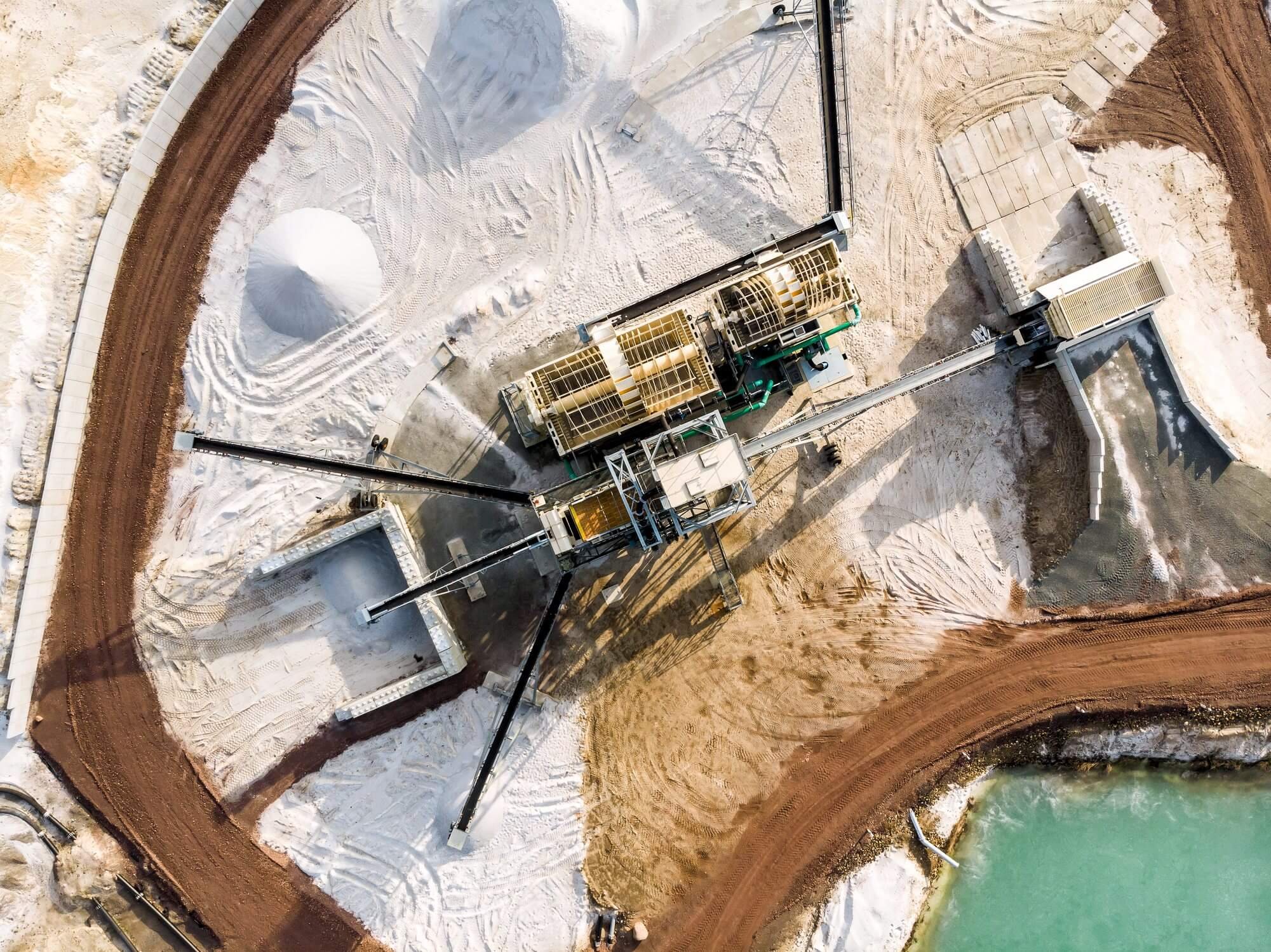
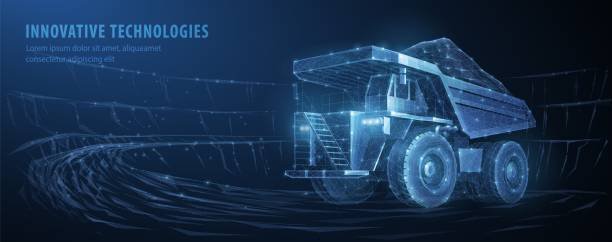

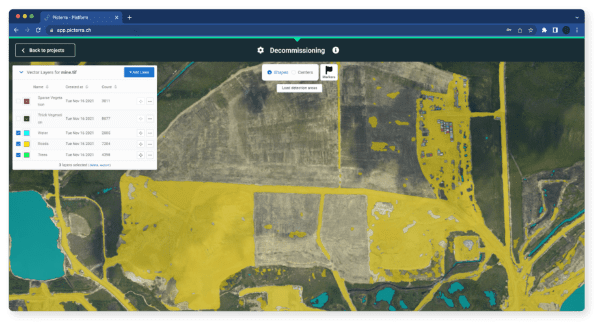
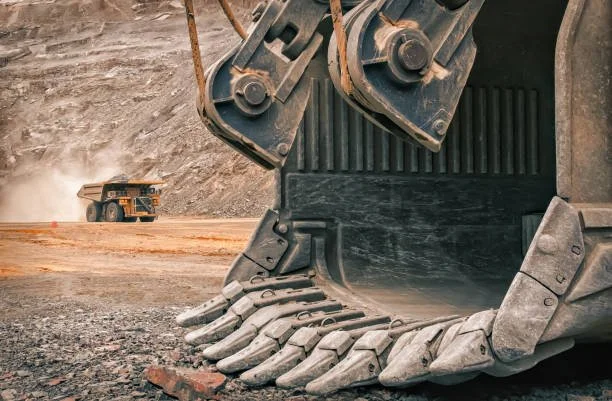
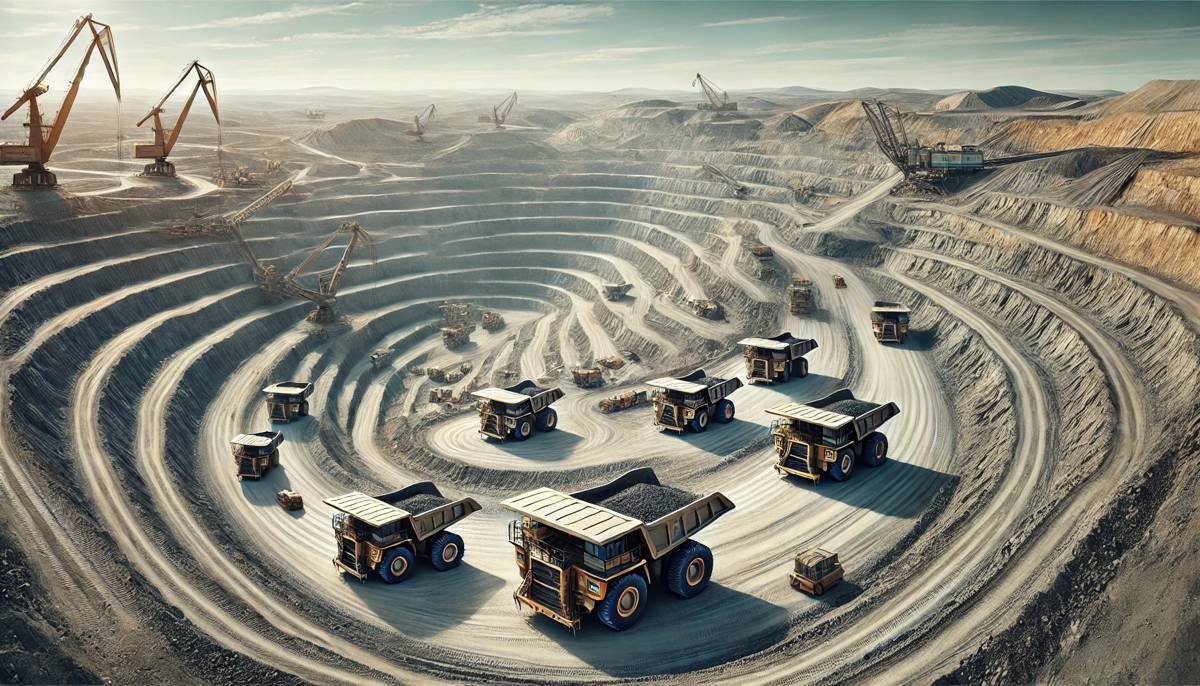

Customer Case Studies
-
Case Study 1: Automated Equipment Monitoring and Maintenance in the Democratic Republic of Congo (DRC)
Client: Major Copper Mining Company
Location: Lualaba Province, DRC
Project Overview:
In the mineral-rich Lualaba Province of the DRC, a major copper mining company faced significant challenges with equipment reliability. Frequent mechanical failures and unscheduled downtimes were leading to costly delays and lost productivity. The company sought a solution to proactively monitor the condition of their heavy machinery to prevent unexpected breakdowns and extend the lifespan of their equipment.
Solution Implemented:
ForeSite AI implemented a comprehensive computer vision system designed to continuously monitor the mining equipment. High-resolution cameras and sensors were strategically placed on critical machinery, including excavators, haul trucks, and drilling rigs. The system was programmed to detect early signs of mechanical issues, such as excessive vibration, overheating, or abnormal wear, by analyzing visual data and sensor readings in real-time.
Key Results:
Reduction in Downtime: The proactive monitoring system led to a 40% reduction in unplanned equipment downtime, significantly improving operational efficiency.Cost Savings: By identifying potential failures before they occurred, the company saved over $2 million annually in maintenance and repair costs.
Extended Equipment Life:
The continuous monitoring allowed for timely maintenance, resulting in a 25% increase in the average lifespan of critical machinery.
Testimonial:"ForeSite AI's automated monitoring system has been a game-changer for our operations. The ability to detect issues before they cause a breakdown has not only saved us money but has also allowed us to maintain a consistent production schedule."
— Maintenance Manager, Copper Mining Company, Lualaba Province, DRC
-
Case Study 2: Worker Safety and Hazard Detection in the United States
Client: Leading Coal Mining Company
Location: Appalachia, USA
Project Overview:
In the coal mines of Appalachia, ensuring worker safety in hazardous environments is a top priority. A leading coal mining company was struggling with maintaining safety compliance and detecting potential hazards in real-time. They needed a robust system to monitor worker behavior, ensure the use of safety gear, and detect environmental hazards such as gas leaks or unstable ground conditions.Solution Implemented:
ForeSite AI deployed a state-of-the-art computer vision system tailored to enhance worker safety. The system included cameras and sensors installed across the mining site, focusing on high-risk areas. The computer vision algorithms were designed to:Monitor workers for compliance with safety protocols, such as wearing helmets and reflective vests.
Detect hazardous conditions, including gas leaks, fire risks, and unstable ground, by analyzing visual data in conjunction with environmental sensors.
Provide real-time alerts to both the workers and the site management team to take immediate action.
Key Results:
Improved Safety Compliance: The system led to a 50% increase in compliance with safety protocols, significantly reducing the risk of accidents.Faster Hazard Response: Real-time hazard detection enabled immediate response, reducing the number of incidents by 35% within the first year of implementation.
Enhanced Worker Protection:
The system's ability to monitor and alert on potential dangers contributed to a safer working environment, with a 20% reduction in injury rates.
Testimonial:
"Since implementing ForeSite AI's worker safety and hazard detection system, we've seen a remarkable improvement in our safety records. The real-time alerts and monitoring have made our operations much safer, and our workers feel more protected."— Safety Director, Coal Mining Company, Appalachia, USA
Big Data
Big Data infrastructures are revolutionizing the mining industry by enabling data-driven decision-making across exploration, operations, safety, and sustainability.
Data Sources: Include exploration surveys, real-time equipment sensors, processing data, environmental monitoring, and market trends.
Storage & Processing: Cloud-based systems and distributed computing handle large volumes of structured and unstructured data.
Analytics: Predictive models forecast equipment failures, optimize production, and enhance resource discovery. Machine learning refines operational processes.
Visualization: Dashboards and 3D models simplify complex data for actionable insights.
Key Benefits:
Efficient Exploration: Improved resource discovery through integrated geological data analytics.
Optimized Operations: Real-time process adjustments for better performance.
Predictive Maintenance: Proactive repairs reduce downtime.
Enhanced Safety: Real-time hazard detection and personnel tracking.
Environmental Sustainability: Data-driven resource use and emission monitoring.
Cost Savings: Lower operational costs through efficiency gains.
Big Data empowers mining companies to improve productivity, reduce risks, and ensure sustainable operations.
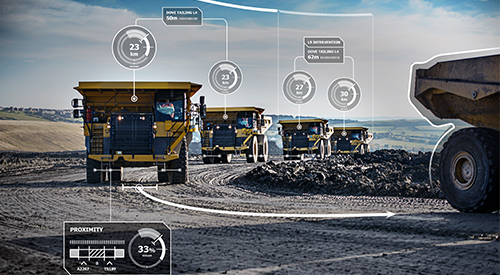
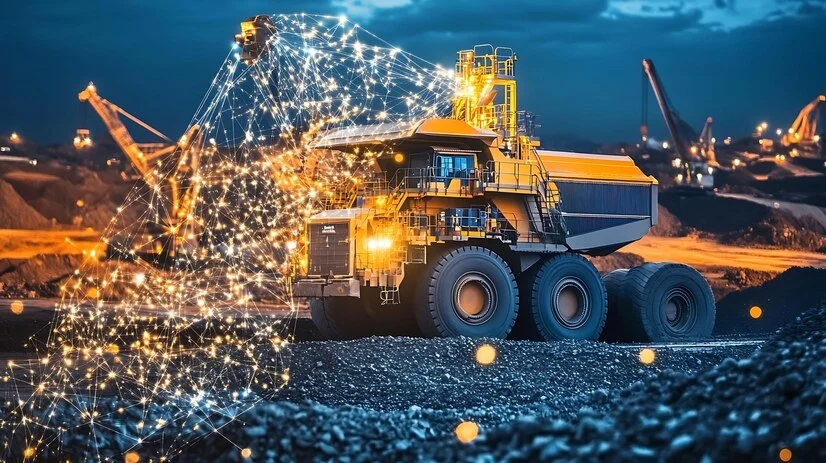
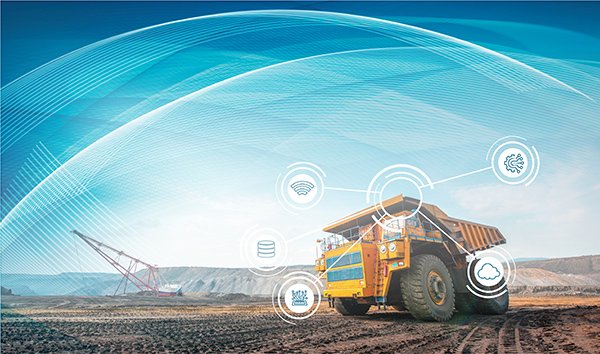
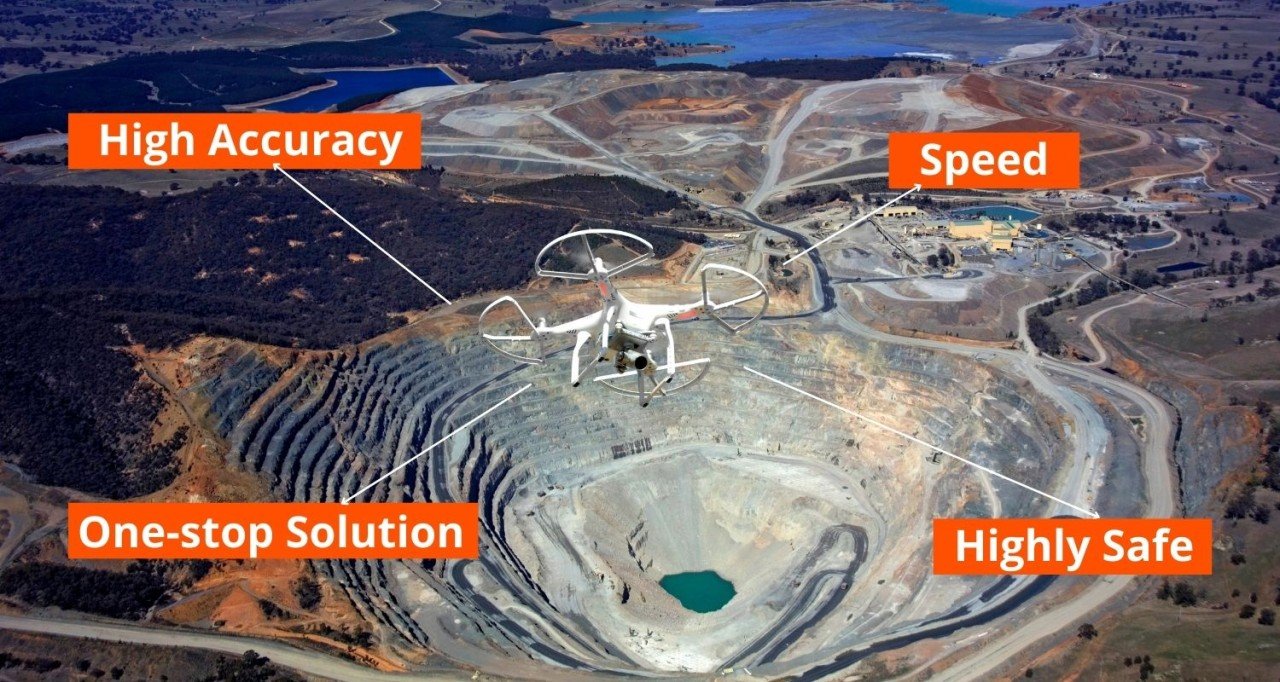
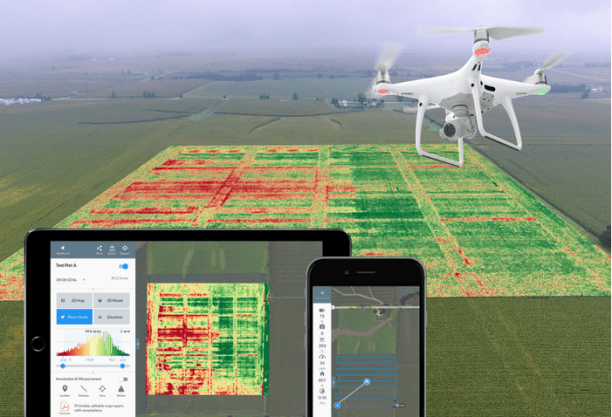
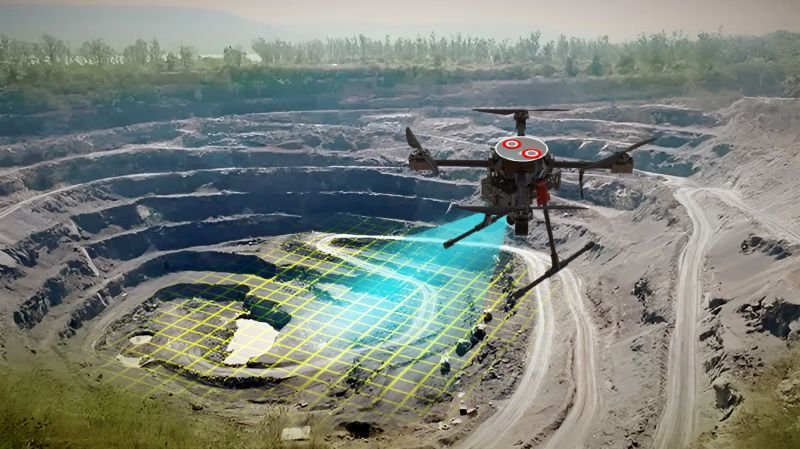
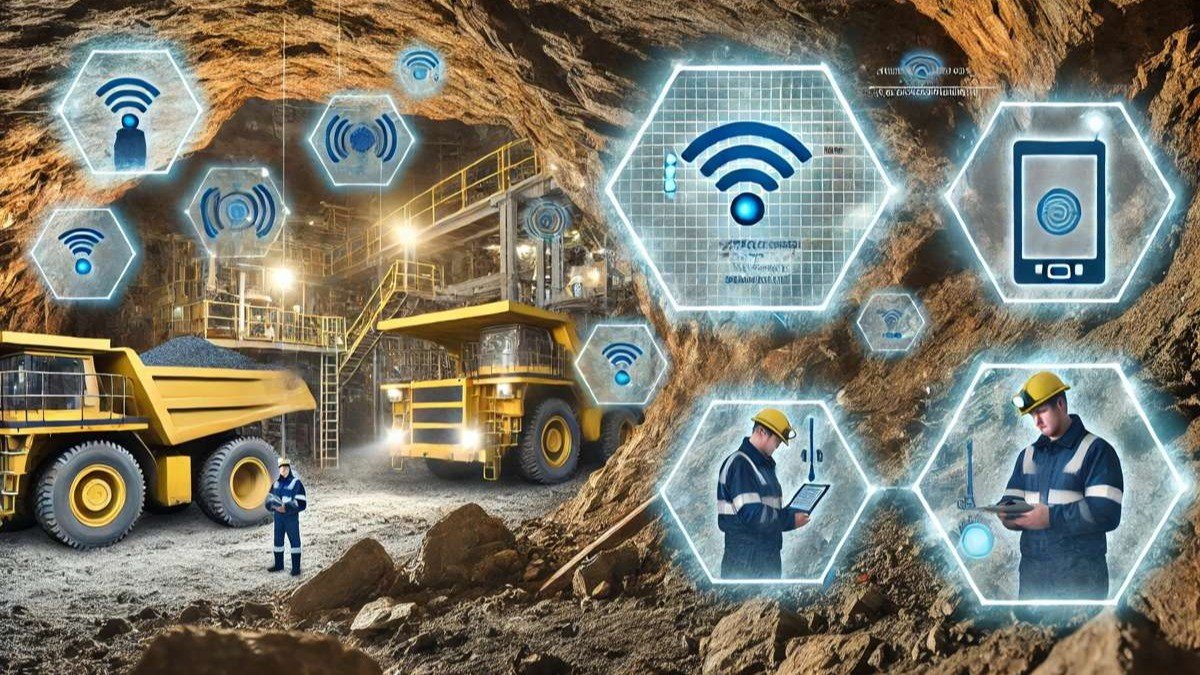
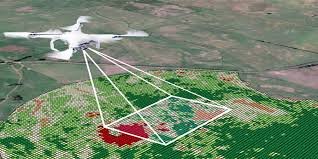




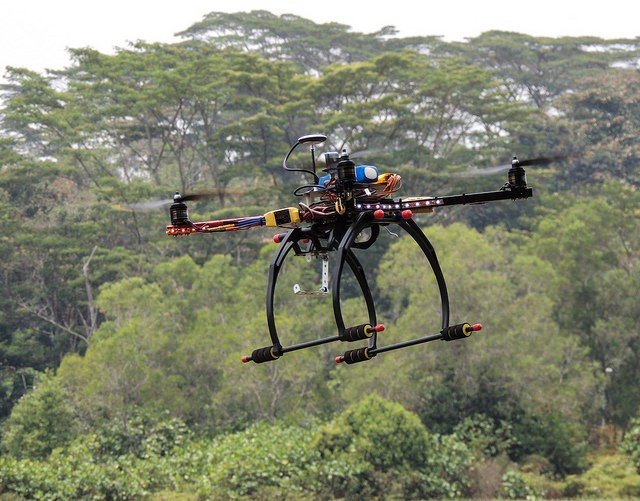
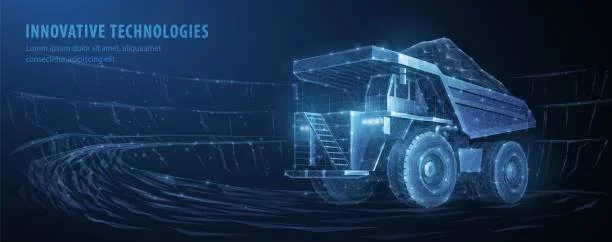
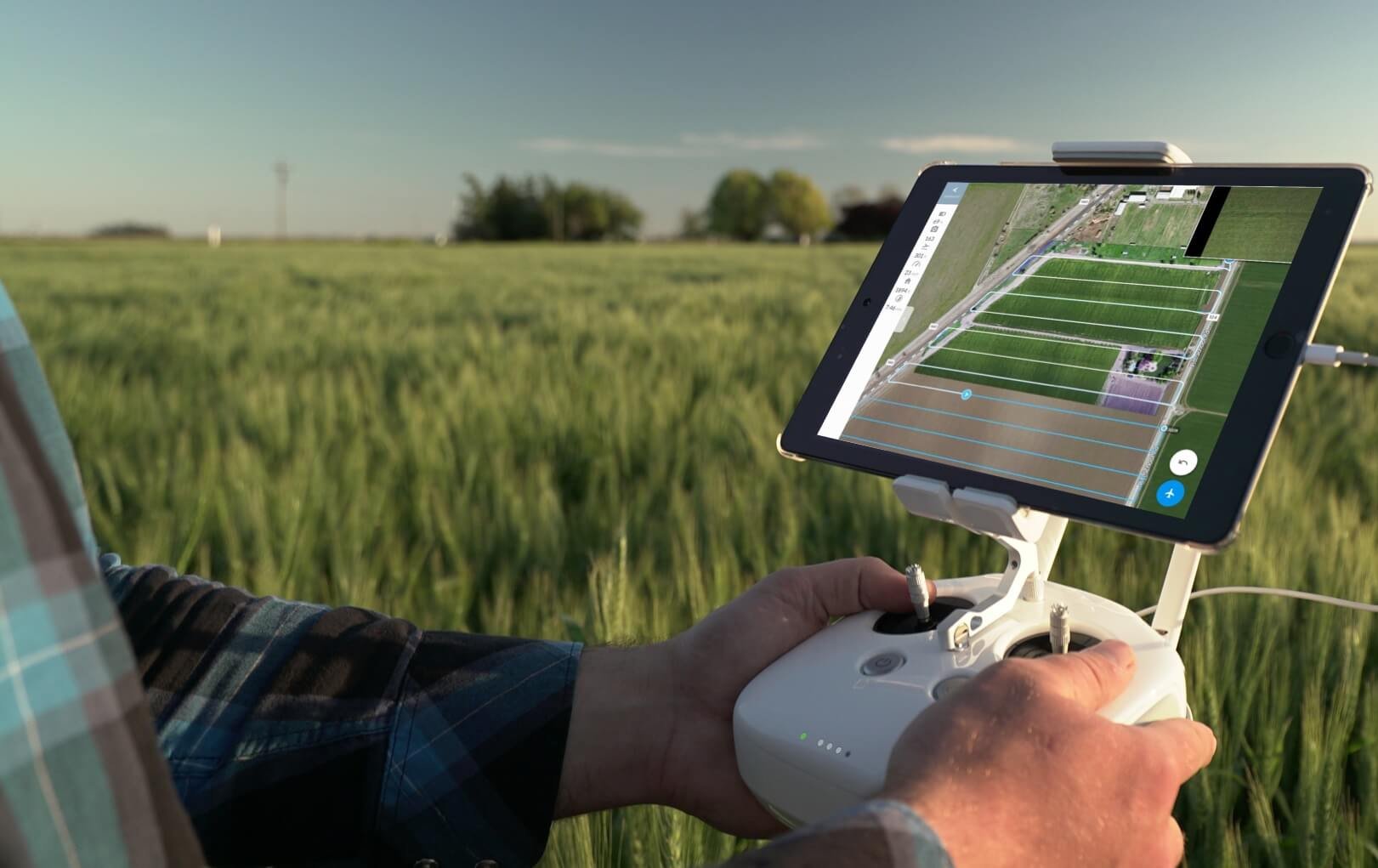